When it comes to silicon wafer fabrication, techniques and their applications vary, along with a complex procedure of purity assessment. How an Indian startup with several patents is revolutionising this? Rajasekar Elavarasan of Raana Semiconductors tells everything to EFY’s Nitisha Dubey.

Q. What is Raana Semiconductors’ specialisation, and who are your target customers?
A. We specialise in manufacturing crystal growth machines, primarily designed for semiconductor-grade silicon wafers and advanced crystals used in defence applications. Our products play a key role in laser-guided missile systems, underwater torpedo launch technologies, range finding and other specialised military applications. Our primary customers include government entities such as the Department of Atomic Energy (DAE), the Defence Research and Development Organisation (DRDO), and the Centre for Materials for Electronics Technology (C-MET), which operates under the Ministry of Electronics and Information Technology (MeitY). We supply crystal growth machines and specialised crystals tailored for electronic fabrication, terahertz applications, atomic radiation detection, and laser production, meeting the advanced technological requirements of these sectors.
Q. Which technique is essential for manufacturing silicon wafers?
A. The Czochralski technique is widely used today to produce silicon ingots, which are essential for manufacturing silicon wafers. The process begins with polysilicon as the raw material. This polysilicon is loaded into a crucible, melting at a high temperature of around 1500°C. A seed crystal is then introduced to the molten silicon, and as it is slowly pulled upward, the silicon transitions from a liquid to a solid state, forming a single-crystal ingot. These ingots typically have a diameter of 300mm and can reach lengths of up to three metres. After the ingot is formed, it undergoes several processing steps, including cutting, lapping and polishing, to transform it into silicon wafers. These wafers are substrates for microelectronic-grade IC fabrication, crucial in producing modern electronic components.
Q. Why is the Czochralski method preferred for producing silicon wafers?
A. The Czochralski method is the dominant technique for producing silicon wafers larger than 200mm. Techniques like the Bridgman method or the Float Zone process are also used for wafers under 200mm. However, the primary limitation lies in the diameter of the silicon ingot, and Czochralski remains the only method capable of producing larger diameter ingots.
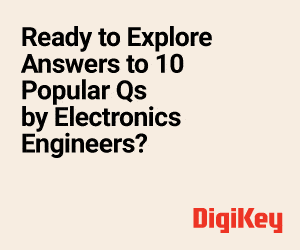
Q. What are the key techniques for producing other advanced semiconductors?
A. Beyond silicon, compound semiconductors like silicon carbide (SiC) are gaining prominence, especially in electric vehicles, where the Physical Vapour Transport (PVT) method is used for production. Similarly, gallium oxide, another emerging material, can be grown using the Bridgman technique, though it is limited to a 50mm diameter. This material shows promise for future semiconductor applications due to the growing focus on electric vehicles. Additionally, sapphire is becoming an important substrate in quantum computing, where photonics-based communication between ICs via laser offers speeds nearly 10 times faster than traditional electronic signals. Sapphire waveguides can efficiently transmit information, which is crucial in enhancing quantum computing performance, where light-based data transport outperforms electron-based methods. These advancements reflect the shift towards high-performance semiconductors and quantum technologies.
Q. How does each technique ensure crystal quality and the overall quality of semiconductor materials?
A. Each technique has its advantages and limitations. The Float Zone method, for instance, eliminates the use of a crucible, minimising contamination as the material never contacts any external surface. This technique produces highly pure and efficient silicon ingots and wafers, but its diameter range is limited. While unsuitable for larger applications, it is ideal for sectors like defence and aerospace, where material efficiency is prioritised oversized. In contrast, the Czochralski method allows for producing larger silicon ingots essential for microelectronic IC fabrication. However, contamination can affect the ingot’s quality as the material contacts a quartz crucible. Strict quality control is applied to both the crucible and raw materials. However, some trade-offs between high purity and larger-diameter wafers are inevitable to meet the semiconductor industry’s demands.
Q. How does the Czochralski technique help reduce impurities in crystal manufacturing?
A. In the Czochralski technique used for silicon manufacturing, it is crucial to maintain low oxygen concentrations in the wafer, as higher oxygen levels introduce impurities. A magnetic field is applied during the process to minimise these impurities. This magnetic field helps draw the impurities, causing them to settle at the bottom of the crucible. We control impurities and oxygen concentration using this process. Additionally, we carefully control the growth rate and thermal gradient to minimise oxygen incorporation in silicon wafers. Our product, a specialised laser crystal, is manufactured using the Czochralski technique, which we intend to supply to the Ministry of Defence (MoD), specifically the Ordinance Factory.
Q. How does the pulling rate impact crystal quality, and why is it critical for wafers?
A. The pulling speed of a crystal varies depending on the material. For example, silicon can be pulled at about 1 mm per minute. However, the pulling rate must be slower, around 0.5mm per hour, for other materials like YAG or other oxide crystals. Exceeding the optimal pulling speed for YAG crystal, such as pulling faster than 0.5mm per hour, can disrupt the formation of a single crystal. This can lead to the inclusion of polycrystalline structures, which degrade the crystal’s quality. Silicon ingots with dislocation are likely to be rejected. Therefore, maintaining the quality of a single crystal throughout the entire 3-metre (10-foot) ingot is essential. Without proper crystal quality, many wafers may be rejected after slicing and wafering due to polycrystalline inclusions.
Q. Why is the Czochralski technique preferred for large-diameter silicon wafer production?
A. The Czochralski technique is the only method capable of producing large-diameter silicon ingots with the desired crystal orientation, matching the ideal single-crystal orientation of the seed. In this process, the oriented seed is dipped into the molten silicon to initiate crystal pulling, ensuring consistent orientation throughout the crystal. Alternative methods, which do not use a seed, result in random crystal orientations. Identifying the desired orientation and extracting the correct diameter from these crystals becomes complex and tedious. This is why the Czochralski technique is preferred for silicon wafers, especially for diameters larger than 20 centimetres (8 inches).
Q. How many wafers are produced from an ingot and prepared for fabrication?
A. Producing a 30-centimetre (12-inch) ingot of approximately 3 metres (10 feet) in length takes about three to four days and consumes around 150 kilowatts of energy per hour. From a single ingot, approximately 6000 to 8000 wafers can be produced. These wafers are then lapped and polished, preparing them for use in semiconductor fabrication.
Q. Do you have any patents?
A. Our company has secured several patents, including one focused on pulling the silicon ingot at a prolonged and controlled rate. The quality of a single crystal largely depends on this pull rate. Our patented system enables us to achieve an extremely low pull rate, as precise as 0.01mm per hour—equivalent to 1/100th of a millimetre per hour. In addition to slow pulling speeds, our system can handle a maximum pull rate of 500mm per minute. This wide range—from 0.01mm per hour to 500mm per minute—is managed using a single motor because of our patented technology.
Another key innovation we have developed is an automatic diameter control algorithm. This algorithm ensures that the diameter of the crystal remains uniform throughout the pulling process, which is critical for both semiconductor and solar industries. The algorithm integrates open-core interface programming with closed-loop proportional-integral-derivative (PID) control systems, allowing precise control over the diameter.
Through this advanced technique, we can produce high-quality monocrystalline silicon ingots. In the silicon industry, two main types of crystals exist: polycrystalline and monocrystalline. However, modern semiconductor and solar applications exclusively use monocrystalline silicon wafers, further underscoring the importance of our technology.
Initially filed in 2019, our patent underwent several hearings before being granted in 2024. This patent covers the minimum pull rate technology and the automatic diameter control algorithm, which are crucial for producing high-quality monocrystalline silicon ingots that meet our customers’ evolving needs.
Q. How is the ND-YAG laser utilised across various industries?
A. ND-YAG, or neodymium yttrium aluminium carbonate, is an oxide crystal capable of generating laser beams. Lasers play a crucial role in various fields, particularly in defence. They are also widely used in medical applications, such as dental surgery, skin care treatments, hair removal, and dermatology. Beyond healthcare, lasers have significant applications in manufacturing, including grinding and cutting processes. Recognising its versatility, we have introduced this India-manufactured laser as one of our key products, initially focusing on military needs, with plans to expand its use to civilian applications.
Q. How do you plan to supply both solar-grade and semiconductor-grade silicon wafers?
A. Currently, our ND-YAG crystals and other crystal machinery are supplied to national government laboratories and research centres. However, we are now scaling up our operations to produce 30-centimetre (12-inch) silicon wafers, aiming to provide both solar and semiconductor-grade wafers. We plan to manufacture solar-grade silicon wafers currently imported from China within the next year. Although solar-grade wafers are of lower quality than semiconductor-grade, they are suitable for solar applications.
Our focus for the first 18 months will be on producing large-diameter solar wafers. After that, we will enhance the Czochralski technique to achieve semiconductor-grade wafers, aiming to complete the process within 36 months. As semiconductor fabs continue establishing themselves in India, there will be increasing demand for high-quality silicon wafers. The goal is to become a leading domestic supplier of these wafers, reduce reliance on imports, and position our company at the forefront of India’s semiconductor manufacturing sector.
Q. What steps are you taking to scale up silicon wafer production in India?
A. Our operations are based in Hosur, Tamil Nadu, where we run a small facility for manufacturing 10-centimetre (4-inch) silicon wafers. With a team of 15 to 20 members, our 280-square-metre (3000-square-foot) startup specialises in silicon wafer production and other crystals, such as ND-YAG and PIEZO crystals, catering to Defence Research and Development Organisation (DRDO) and atomic energy requirements.
We are scaling up, supported by grants from the MoD, to produce laser and semiconductor-grade crystals. Additionally, we are pursuing private equity funding, primarily from venture capitalists, to expand our operations further. We aim to become the first company in India to manufacture solar-grade silicon wafers domestically, with plans to achieve this within 18 months. Following that, we strive to transition to semiconductor-grade wafer production. Over the past eight to nine years, we have supplied 26 machines to various government organisations. We are committed to accelerating our progress to become pioneers in India’s silicon wafer manufacturing industry.
Q. How does Raana Semiconductors manage component sourcing to ensure efficient production and high quality?
A. We handle core system development in-house while outsourcing processes like ASME (American Society of Mechanical Engineers) standard welding, machining, and other fabrication activities. Hosur, an industrial hub with a strong presence in the automobile sector and precision engineering, including TVS, Ashok Leyland, and TATA, offers a well-established vendor ecosystem specialising in high-precision machinery and components. This allows us to outsource mechanical parts based on our designs for external fabrication.
Once the parts are ready, we assemble them at our facility, perform critical tasks like graphite hot zone assembly, and implement PLC (programmable logic controller) programming and automatic diameter control algorithms—capabilities that set us apart from other companies. Establishing an in-house plant for these operations would be costly, so outsourcing reduces expenses and supports micro-enterprises in Hosur.
Q. How do you ensure vendor quality and scalability for wafer production and semiconductor manufacturing equipment?
A. We currently have around 50 vendors and are working to increase this number to support the production of wafers and wafer manufacturing equipment. Expanding our vendor base will help us meet production timelines and secure competitive pricing. Our focus is on identifying reliable vendors to scale up our operations efficiently.
In semiconductor manufacturing, all components must be fabricated to meet specific standards, such as being corrosion-resistant, clean room and vacuum-compatible. Additionally, specific parameters, like maintaining Ra values for good surface finish, must be closely monitored. For components like graphite heaters, high-purity graphite is crucial, with impurity levels kept to a minimum and purity reaching approximately five ppm. We rigorously validate vendors based on material purity and manufacturing processes to ensure they deliver high-quality products.
Q. What challenges hinder India’s progress in semiconductor manufacturing development?
A. A key challenge is ensuring a stable power supply for semiconductor manufacturing. Additionally, there is a growing need to meet the demand for skilled manpower. Securing critical components presents another hurdle, as some countries strategically limit exports, pushing us to develop these parts domestically. This process will take time and effort to yield the desired results.
Despite these obstacles, I remain confident in the capabilities of the Indian scientific community and the strong support from the government. With sustained efforts, we anticipate overcoming these challenges within the next two to three years. Looking ahead, India has the potential to become a global leader in semiconductor manufacturing within the next five years.
Q. What are your primary focus areas for the future?
A. Our focus is on producing semiconductor-grade silicon wafers to meet future industry demands. With companies like Tata-PSMC, Micron, LAM Research and others establishing fabrication units across India, the need for local wafer production is rising. India’s electronics manufacturing has tremendously progressed through backward integration, from assembling smartphones to packaging integrated circuits (ICs), with 40% of IC value now added locally.
Over the next two to three years, full-scale IC fabrication, including wafer lithography, is expected in India. Aligned with our vision, we strive to develop high-quality wafers to support the future of semiconductor manufacturing. Our goal is to achieve self-reliance across the entire value chain—from wafer production to the manufacturing of end-semiconductor devices—by 2028-2030.
Q. How did the business perform in terms of growth during the last fiscal year?
A. We are right on track. With nearly 30% growth and a solid pipeline of orders from defence and MeitY, ranging between ₹120 million and ₹150 million for 2025-26, we aim for a turnover of ₹200 million in the same period. Plus, as we dive into manufacturing solar-grade equipment and wafers, we are looking at generating an impressive ₹3 billion to ₹4 billion in revenue.