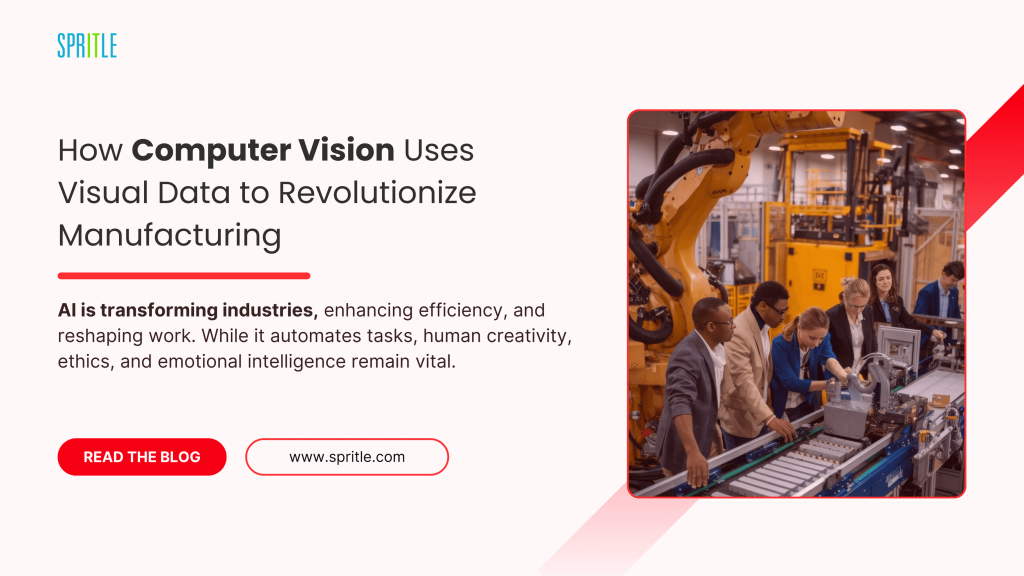
The manufacturing industry is at the forefront of technological evolution, embracing innovations that streamline operations, enhance quality, and reduce costs. Among these, computer vision has emerged as a pivotal technology, leveraging vast volumes of visual data to drive actionable insights and automation. Powered by advancements in artificial intelligence (AI), machine learning (ML), and deep learning (DL), computer vision enables machines to perform tasks traditionally reliant on human perception.
This blog explores how computer vision transforms manufacturing through advanced applications, technical workflows, and real-world examples.
What is Computer Vision?
At its core, computer vision involves enabling machines to interpret and process visual data—images, videos, or 3D environments—to extract meaningful insights. This is achieved through sophisticated algorithms and AI frameworks, such as convolutional neural networks (CNNs) and vision transformers (ViTs). These systems mimic the way humans recognize patterns and make decisions based on visual inputs but do so with enhanced precision, scalability, and speed.
Key Components of Computer Vision in Manufacturing
- Image Acquisition: Capturing data through high-resolution cameras, LiDAR sensors, or hyperspectral imaging devices.
- Preprocessing: Techniques like noise reduction, image normalization, and data augmentation ensure clean and usable input data.
- Feature Extraction: Using algorithms like Scale-Invariant Feature Transform (SIFT) or Histogram of Oriented Gradients (HOG) to identify critical image features.
- Model Inference: Deep learning models such as YOLO (You Only Look Once) or Faster R-CNN for object detection, segmentation, or classification.
- Post-Processing and Analysis: Interpreting model outputs to drive actionable insights and real-time decision-making.
Applications of Computer Vision in Manufacturing
1. Automated Quality Control (QC)
Traditional QC processes often depend on manual inspection, which is time-intensive and prone to errors. Computer vision systems automate this by:
- Defect Detection: Using image segmentation and anomaly detection algorithms to identify cracks, scratches, or discolorations. Advanced techniques like semantic segmentation ensure pixel-level accuracy.
- Dimensional Verification: Employing 3D vision systems to measure tolerances and ensure compliance with CAD designs.
- High-Speed Inspection: Systems like Cognex In-Sight can inspect hundreds of items per minute, ensuring quality without interrupting production flow.
For instance, semiconductor manufacturers use vision systems to detect micro-level defects in silicon wafers, leveraging CNNs trained on thousands of defect patterns.
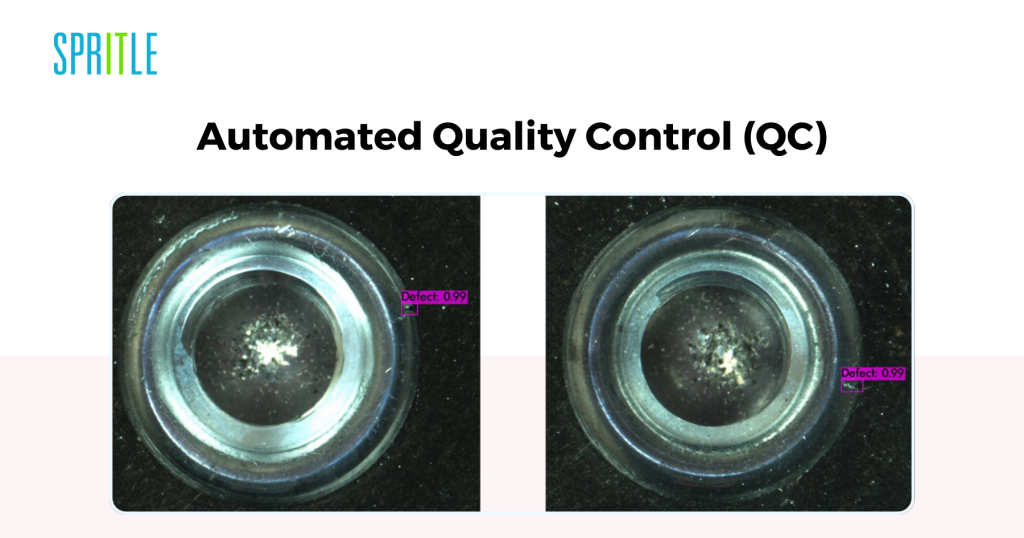
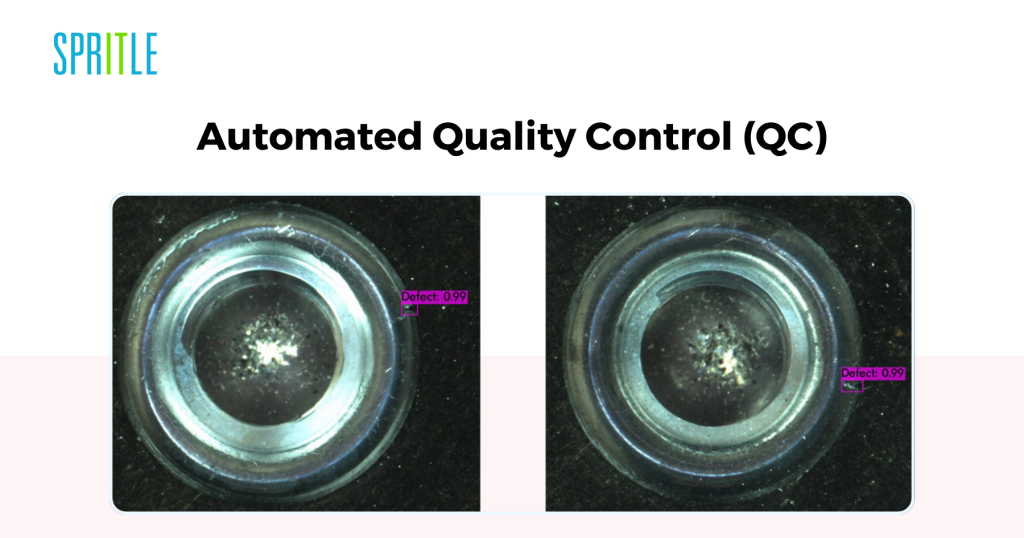
2. Predictive Maintenance
Unscheduled downtime can cost manufacturers millions annually. Computer vision facilitates condition-based maintenance by analyzing visual data from machinery.
- Thermal Imaging: Detects overheating components using infrared cameras, flagging potential failures.
- Vibration Analysis: High-speed cameras track deviations in motion patterns, predicting mechanical faults.
- Wear Monitoring: Vision systems capture minute wear patterns on tools, enabling replacements before breakdowns.
A practical example is Airbus, which employs drones equipped with vision systems to inspect aircraft for structural anomalies, reducing maintenance times by over 90%.
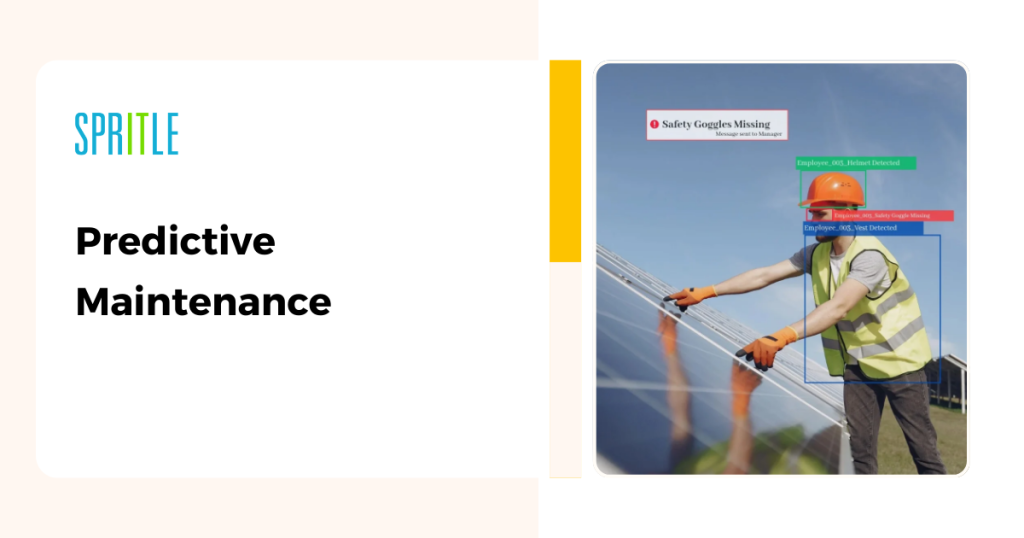
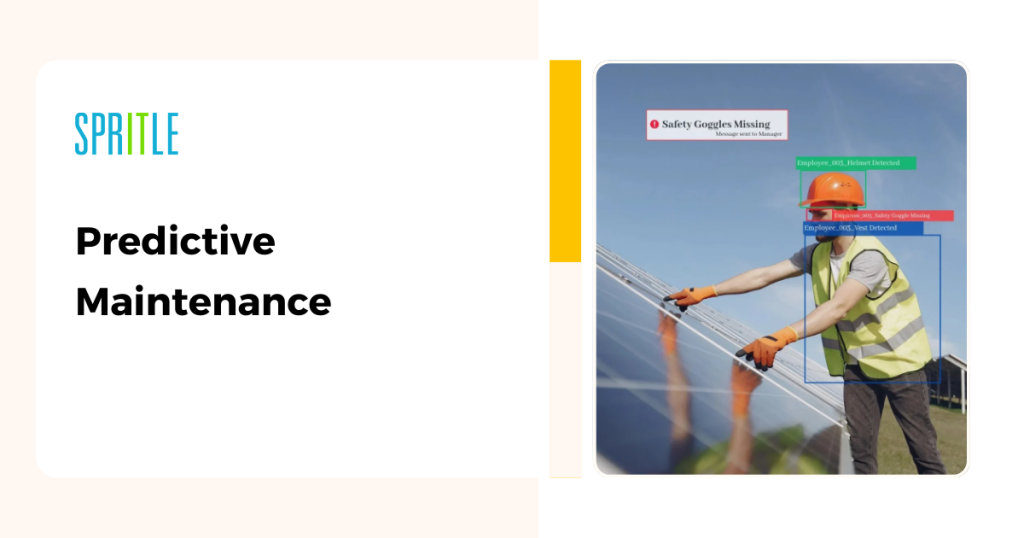
3. Worker Safety and Compliance
Ensuring worker safety in hazardous environments is a priority. Computer vision improves safety compliance through:
- PPE Detection: Models trained on datasets like Open Images or custom datasets detect whether workers wear safety gear, such as helmets or gloves, in real-time.
- Behavioral Analysis: Cameras monitor movements, identifying unsafe practices such as proximity to dangerous machinery or unauthorized zones.
- Incident Detection: Systems detect emergencies like fires, spills, or collapses and trigger automated alerts.

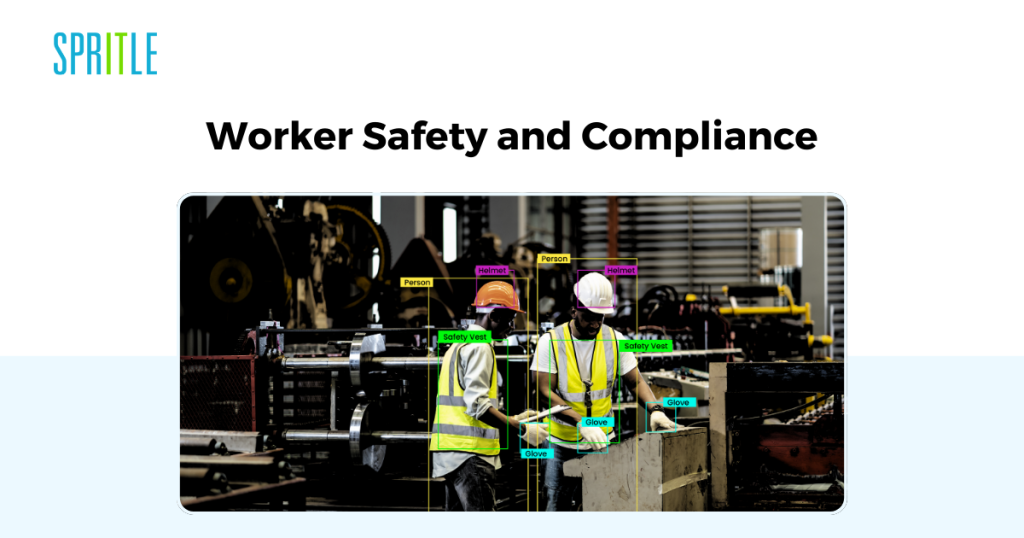
4. Inventory and Warehouse Management
Efficient inventory management is essential for uninterrupted production. Computer vision enhances logistics with:
- Real-Time Tracking: Vision-guided robots navigate warehouses, scanning barcodes or QR codes to update inventory systems.
- Shelf Monitoring: Cameras combined with object recognition track stock levels, automatically alerting for restocking.
- Load Verification: Vision systems confirm that packages are accurately labeled and loaded for shipment, reducing errors.
A leading example is Amazon’s fulfillment centers, where computer vision-guided robots collaborate with humans to streamline warehouse operations.
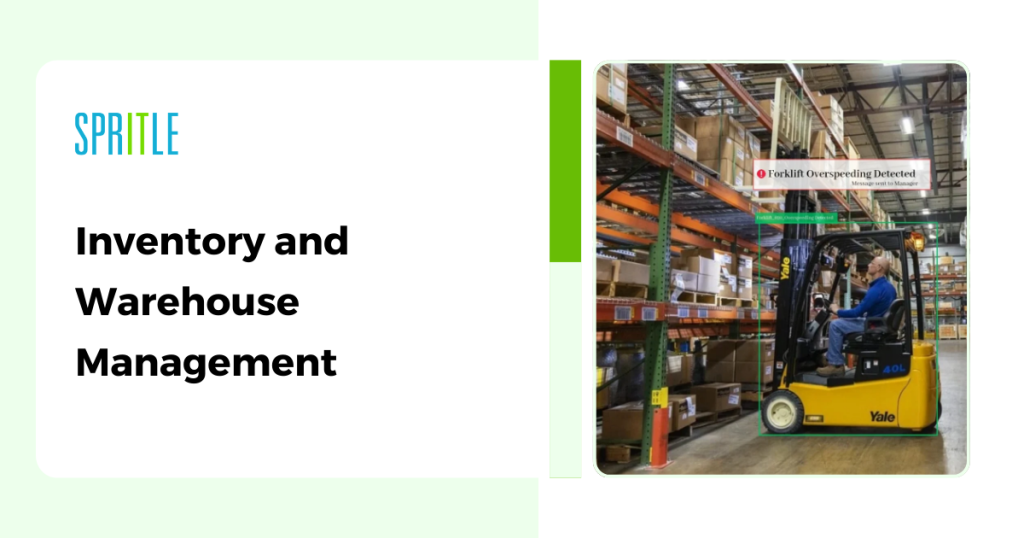
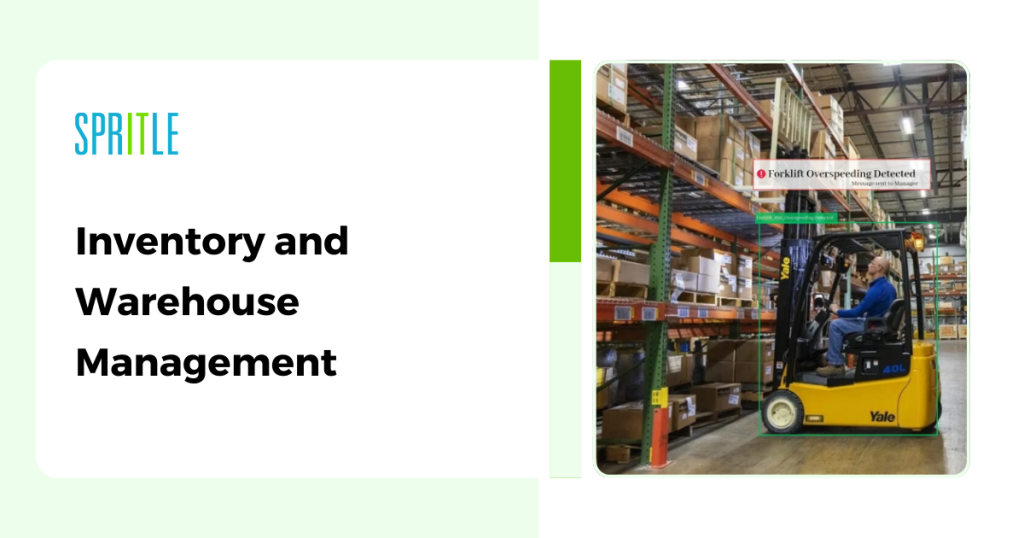
5. Process Optimization and Robotic Integrations
Computer vision seamlessly integrates with robotics to optimize manufacturing processes. Use cases include:
- Collaborative Robots (Cobots): Cobots equipped with vision systems handle complex tasks like assembly, welding, or material handling while adapting to dynamic conditions.
- Real-Time Feedback: Vision systems monitor production lines, identifying bottlenecks and providing data to refine workflows.
- AI-Powered Sorting: Automated systems sort products by size, color, or shape, often using reinforcement learning for continuous improvement.
Tesla’s Gigafactories employ vision-guided robotics extensively, optimizing vehicle assembly with minimal human intervention.
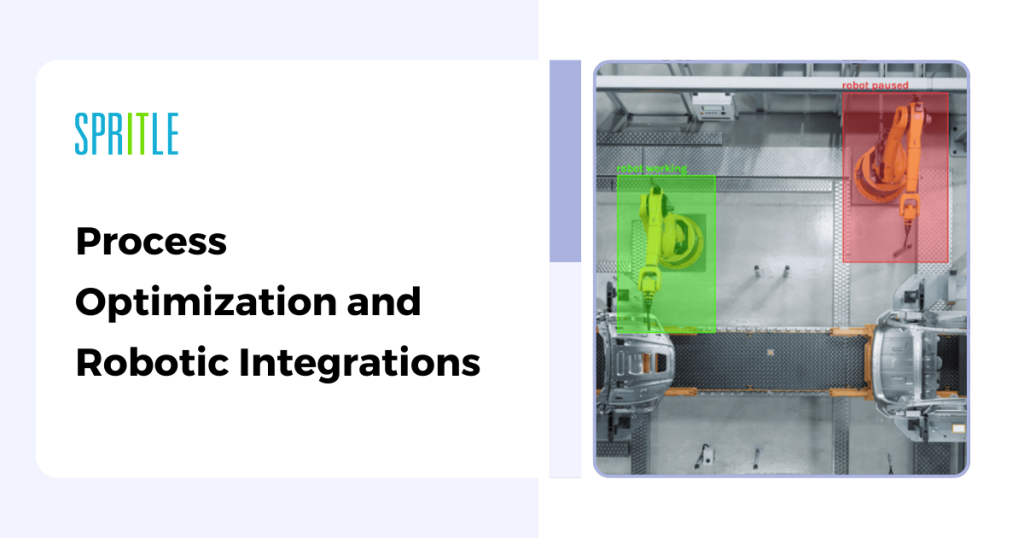
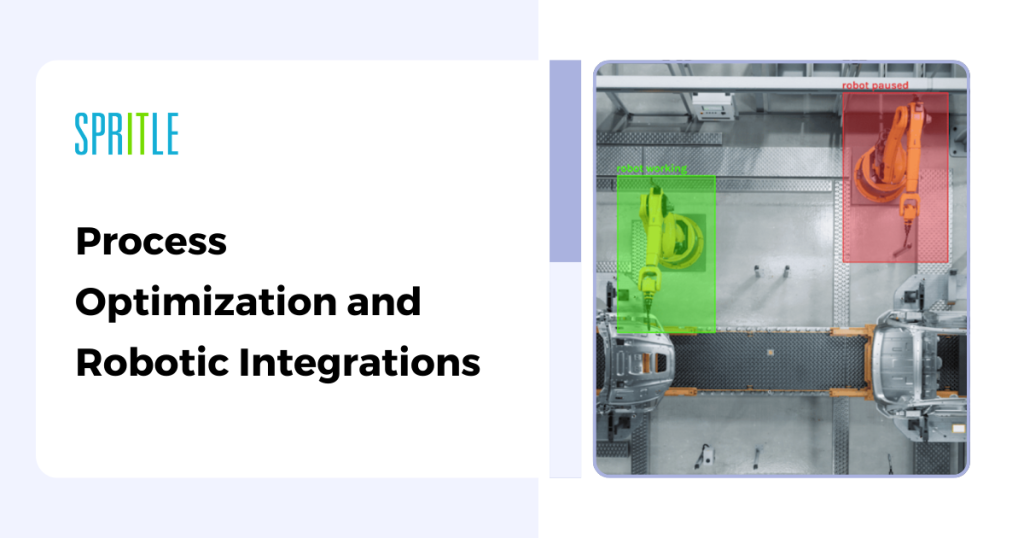
Technical Workflow of Computer Vision in Manufacturing
The implementation of computer vision follows a structured workflow:
- Data Collection:
- Install high-resolution cameras and sensors to capture visual data.
- Use distributed edge devices for local processing or centralized cloud systems for complex analyses.
- Model Development:
- Choose appropriate AI models based on the task (e.g., ResNet for image classification, Mask R-CNN for segmentation).
- Train models on diverse datasets using frameworks like TensorFlow or PyTorch.
- Augment datasets with synthetic images to improve robustness.
- Deployment:
- Use edge AI devices like NVIDIA Jetson for low-latency tasks or cloud platforms like AWS for large-scale processing.
- Implement APIs to integrate vision systems with Manufacturing Execution Systems (MES) or Enterprise Resource Planning (ERP) software.
- Continuous Improvement:
- Monitor model performance metrics such as precision, recall, and latency.
- Update models regularly to adapt to new production scenarios or defect patterns.
Challenges and Future Directions
Key Challenges
- Data Volume and Quality: Capturing high-quality, labeled datasets is resource-intensive.
- Integration Complexity: Aligning vision systems with legacy manufacturing processes can be challenging.
- Real-Time Processing: Achieving low-latency inference, especially in high-speed environments, requires robust edge computing infrastructure.
Future Directions
- Edge AI Expansion: On-device processing with minimal latency will drive applications in real-time quality control and safety monitoring.
- 3D Vision Systems: With advancements in LiDAR and stereoscopic imaging, manufacturers can achieve greater depth perception and accuracy.
- Explainable AI (XAI): As AI-driven vision systems become critical to decision-making, ensuring transparency and trustworthiness will gain importance.
- Integration with Digital Twins: Computer vision will augment digital twin models, providing real-time feedback for simulations and process optimizations.